Олег груненков, руководитель проекта lada xray («колеса.ру»)
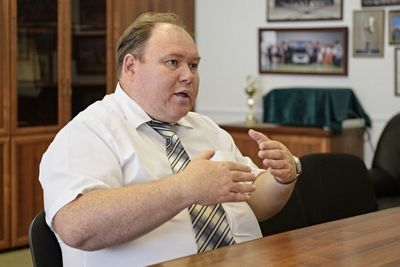
В то время, когда правильная дата запуска Xray в производство? Что неспециализированного у него с моделями Volkswagen? какое количество готово предсерийных экземпляров, и как их испытывают? Мы пообщались с начальником проекта Xray Олегом Груненковым.
— Олег Евгеньевич, в какой стадии на данный момент находится проект, что удалось сделать, и что будет происходить в скором будущем?
— Проект идёт четко в соответствии с графиком, что мы выяснили в конце прошлого года. Напомню, что мы тогда на пара месяцев сократили сроки запуска автомобиля: в случае если раньше мы говорили, что старт производства автомобиля у нас будет в начале 2016 года, то на данный момент мы определились с датой – до 15 декабря 2015 года мы запустим автомобиль в производство. Очень важный этап, что на данный момент начался, – это сборка так называемых VС-какое количество (пробная партия машин, служащая для испытаний и подготовки производства, с заведомо более низким качеством сборки, которое растет по мере приближения к серийному выпуску автомобилей для продажи, – прим. ред.).
Это, по сути, первые «физические» машины, каковые мы собираем на площадке Умело-промышленного производства (ОПП АВТОВАЗа). Но мы максимально задействуем действующие производства [основных мощностей завода], каковые делают нам фактически все нужные компоненты.
При разработке автомобиля был использован самый новый стандарт Альянса (Renault-Nissan – прим.ред.), в соответствии с которым многие работы сделаны виртуально, и исходя из этого очень многое должно быть сделано чуть раньше, чем это было по ветхим стандартам. К примеру, главная подготовка производства по сварке кузова была совершена ещё в начале этого года, и мы уже с марта начали варить кузова по большей части производстве.
Новый стандарт показывает, что кроме того самые первые кузова должны вариться уже по большей части производстве. Это принципиальный момент, по причине того, что ни разу мы не делали таких вещей как раз для новых машин. Для «фейслифтов» (обновлённых вариантов уже существующих моделей – прим.ред.) делали – в том месте это естественно, в то время, когда вы меняете всего лишь последовательность подробностей.
Но для новых машин, каковые имеют больше половины уникальных сварки и деталей штамповки, мы для того чтобы ни при каких обстоятельствах не делали.
Высокие требования по качеству стоят перед отечественными производствами. К примеру, чтобы собрать VС-Lot, мы отрабатывали сварку, собирали пара десятков кузовов, настраивали оборудование, и цель была – взять точность кузова по замерам 75%. Другими словами 75% контрольных точек должны чётко попадать в допуск подробностей (не отклоняться от правильных размеров, заданных в проекте, – прим.ред.).
Я честно скажу – раньше у нас такое требование было к товарным машинам. на данный момент же на АВТОВАЗе сильно изменились требования по качеству изготовления кузова серийных автомобилей – Альянс Renault-Nissan требует 92%. Но мы решили, что при контроле сборки товарных автомобилей мы будем наблюдать на отечественных соперников, заберём стандарты Volkswagen, где требование 95%. И по сей день готовые к отправке в салоны машины Granta, Kalina, Datsun уже полностью соответствуют этому требованию, кузова весьма правильные.
Отечественная цель – на серии VС-Lot проекта Xray взять уже максимально правильные кузова, минимум 75%. Не смотря на то, что по факту мы имеем 77%, и это залог того, что все главные подробности смогут весьма совершенно верно устанавливаться на данный кузов, и в то время, когда дело дойдет до товарных машин, то мы дотянем до германских 95%. Чем правильнее кузов, тем понятнее обстановка по автомобилю, тем правильнее результаты сборки и результаты испытаний, тем будут вернее приняты решения по доработке той либо другой оснастки.
— Что из себя воображает сборка VС-Lot?
— По сути, это мелкий конвейер в ОПП, имеющий 9 постов сборки, на каковые мы берём окрашенный кузов и начинаем на него устанавливать элементы и определённые детали. Машина планирует приблизительно в течение 5-6 рабочих смен. По окончании того, как мы всецело собираем автомобиль, у нас остаётся ещё пара постов: регулировки, заправки и программирования жидкостями.
Исходя из этого потом мы перемещаем автомобиль из ОПП на главную линию сборки «B0» («B0» – платформа Renault-Nissan – прим. ред.) и производим заправку жидкостями, статическое и динамическое программирование автомобиля, опробование на динамических роликах, и совсем «отстраиваем» все машины, ликвидируя все неточности, если они имеется. Другими словами пара дней автомобиль ещё проводит на линии «B0», и в том месте мы проводим все финишные операции сборки.
— какое количество машин в серии VС-Lot?
— У нас запланировано 23 автомобиля, 28 порядка и кузовов 21 юнита. Юниты – это части кузова. К примеру, мы разделяем кузов на две части, переднюю и заднюю, доукомплектовываем переднюю часть панелью устройств, заднюю – задним сиденьем и ремнями безопасности и раздельно проводим какие-то опробования.
Всего у нас предусмотрено 63 кузова, часть из которых мы делим на юниты.
Кузова нам уже на данный момент делает сварочное производство. Окраска кузовов происходит по главной линии. Мы фактически уже совершили подготовку производства, доработали все скиды (скид – рама, на которой закрепляется кузов перед погружением в окрасочную ванну, – прим. ред.) и доработали всё ПО по траекториям перемещения кузова.
Другими словами на данный момент остались лишь тонкие настройки, каковые мы совершим, заканчивая подготовку производства, – я пологаю, что до конца лета мы этим ещё позанимаемся, улучшим уровень качества.
— На чем на данный момент делается выговор в подготовке производства?
— на данный момент мы сконцентрированы на следующих моментах. Траектория нанесения мастик – достаточно трудоёмкий и весьма правильный процесс, и мы обучаем персонал в данной области. Отрабатываем небольшую оснастку, которая нужна конкретно в линии окраски, – прочие элементы и небольшие упоры, каковые разрешают нам чётко фиксировать элементы кузова.
По бамперной группе подробностей на стадии производства VC-Lot 97% всех подробностей приходят уже от тулмейкеров и от отечественных поставщиков с главной оснастки (другими словами компоненты – от серийных автомобилей, а не со штучного умелого производства – прим. ред.). на данный момент мы приобретаем все бампера от отечественных тулмейкеров, изготовителей оснастки, ну а окрашиваем бампера уже в главной линии Производства пластмассовых изделий (ППИ АВТОВАЗа). Так, ППИ уже кроме этого вовлечено в процесс сборки VC-Lot.
— Но сборку VC-Lot нельзя назвать серийным производством? Как эти автомобили далеки от серийных?
— До тех пор пока мы говорим «главная оснастка», а не «главный процесс», не серийное производство. К примеру, у нас уже имеется пресс-форма, на ней отлита панель устройств, но эта панель пока не имеет тиснения – данной шероховатости, которая приятна на ощупь. на данный момент нам принципиально важно постараться собрать автомобиль и отыскать те решения, каковые требуют улучшения. В случае если нам потребуются улучшения, мы дорабатываем оснастку и лишь затем наносим это финишное тиснение.
Двигатели, коробки передач и заднюю подвеску мы собираем по большей части производстве. Так, целый завод на данный момент как бы сконцентрирован на сборке VC-Lot. Это довольно высокий уровень локализации.
И 97% подробностей с главной оснастки на данном этапе, о которых я сказал, – это довольно высокий показатель.
Да, 3% – это так именуемые подробности «первого съёма», первые подробности, ещё требующие доработки, каковые делаются на прототипной экспериментальной оснастке. Но, по стандартам Renault, подробностей с главной оснастки на этом этапе должно быть 85%, а мы имеем 97%. Исходя из этого автомобиль, по сути, получается достаточно правильным.
В ходе сборки VC-Lot мы решили, что будем максимально тестировать все жгуты проводов. Исходя из этого у нас имеется особый стенд, что мы изготовили вместе с Альянсом и на котором мы тестируем 100% жгутов проводов. По сути, это все электрические компоненты автомобиля без кузова.
Другими словами они развешаны на особом стенде, разложены на стеллажах – светотехника, отопитель, кондиционер, стеклоподъёмники, сигнализация, электронная педаль газа плюс имитация силового агрегата посредством компьютера. Другими словами комплект компонентов, на основании которого возможно подключать все жгуты и тестировать, не ставя на автомобиль.
— Нервная совокупность автомобиля
— Да-да! И что принципиально важно – не нужно разбирать автомобиль, в случае если у нас имеется неприятности с данной совокупностью. Так как жгуты проводов укладываются прежде всего, позже шумоизоляция, позже всё другое, и на выходе мы имеем неприятности. В новой ситуации мы так не делаем.
Мы тестируем жгуты проводов, а затем начинаем сборку автомобиля.
И у нас оказалось, что в первом автомобиле на программировании было распознано практически 10 неточностей, пять из которых мы сходу устранили, а над пятью оставшимися на данный момент трудимся. Но на опробования мы израсходовали минимум времени – закладывали семь дней, а сделали всё за сутки. И такие новые подходы, в то время, когда на ранних стадиях мы контролируем и контролируем обстановку и не допускаем сборку из некачественных подробностей кроме того на VC-Lot, разрешают нам достаточно скоро делать подробности.
на данный момент мы выходим на темп «один объект в день». Или один автомобиль, или один кузов. Многие кузова фактически имеют состав автомобиля, лишь без двигателя. Они с интерьером, кроме того на колёсах – речь заходит лишь о том, что у них будут статичные опробования: по интерьеру либо, к примеру, по надёжности закрывания дверей.
Двигатель в том месте не нужен, исходя из этого мы его не устанавливаем. Ежедневно мы делаем по одному такому объекту.
— В какой момент Xray обязан «переехать» из ОПП на основной конвейер?
— По отечественному графику мы это сделаем сразу после шат-дауна (летнего корпоративного отпуска на АВТОВАЗе – прим.ред.), что будет с 25 июля по 15 августа. Другими словами у нас будет 20 дней отпусков на заводе, и, когда мы выходим, мы сходу начнём сборку кузовов на главной линии. Но, само собой разумеется, мы попытаемся протестировать автомобиль на сборке ещё в июле, дабы готовиться к запуску автомобиля на главном конвейере.
Как я уже сообщил, часть финишных операций сборки мы уже делаем на конвейере, а часть лишь будем пробовать.
Вероятнее, пара «предтестовых» машин мы соберём ещё в июле. До тех пор пока данный вопрос обсуждается, но за июль мы в обязательном порядке подготовим отечественные производственные линии. По причине того, что график хватит плотным – мы должны будем собрать порядка 68 машин за полтора месяца и отработать производственные процессы уже на линии.
— А имеется уверенность в том, что всё окажется?
— Да. Мы забрали 20 человек рабочих, каковые в большинстве случаев трудятся на линии «В0», и послали их получать образование ОПП. на данный момент они сами собирают машины Lada Xray в ОПП. Все они потом станут или бригадирами, или наставниками вторых рабочих. Мы планируем до 28-й семь дней отработать все нужные объекты VC-Lot, и машины, и кузова, и затем эти люди уже придут и будут готовить рабочие места для главного производства.
Эти люди станут «коучами» – преподавателями, наставниками для других рабочих, они будут обучать рабочих сборке. на данный момент они набивают руку в ОПП, а позже придут на главный конвейер.
— У Lada Vesta имеется правильная дата запуска в производство – 25 сентября. А у Xray?
— До 15 декабря. Эту дату мы уже заявили на одном из автосалонов. Президент чётко озвучил дату – 15 декабря.
Причем мы думаем, что это критичная дата, самый последний срок. И мы весьма серьёзно настроены именно на текущий год
«Колеса.ру»