Как автопроизводители снижают вес своих автомобилей
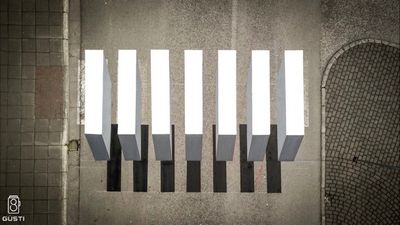
Вот, что производители машин имеют ввиду под термином «понижением веса»
Производители машин применяют хитроумные уловки чтобы максимально скинуть вес со собственных моделей машин. Разглядим, как они это делают на примере GM.
Независимо от того, на чем вы едите, правила игры будут однообразными: чем больше машина весит, тем больше энергии требуется, дабы перемещать ее в пространстве. Это указывает, что нужно больше топлива, а повышение сгорающего бензина/дизеля увеличивает количество выбросов. Потому, что экологические нормы всегда ужесточаются, автопроизводителям приходится выискивать возможности ставить собственные транспортные средства на «диеты», дабы максимизировать эффективность их применения, как это вероятно на нынешнем этапе развития разработок.
Дженерал моторс, как и другие производители машин идет по тому же пути понижения веса собственных машин, в движение идут новейшие материалы и разные технические улучшения конструкции.
Смотрите кроме этого: Производители машин снижают вес машин
Мы думаем, что не бывает универсальных материалов для автомобилестроения, заявил Чарльз Клейн, эксперт несущий ответственность за глобальную стратегию уменьшения выбросов CO2 в GM. Суть этого заявления истолковать легко, в каждом транспортном средстве на данный момент употребляется смесь разных металлов и пластиков, а также созданных на базе углеродного волокна. Кроме того всецело алюминиевый Ford F-150, что так обожают позиционировать как всецело алюминиевый пикап, в собственной базе металлическую конструкцию.
С первого взора думается, что задача перед производителями машин стоит несложная и для ее решения требуется мало. Вычислить самые легкие материалы для автомобиля, интегрировать их в конструкцию автомобили и дело будет решено. Но присмотревшись внимательнее окажется, что дело обстоит куда как сложнее.
Во-первых, выбранное сырье должно быть не только легким, оно должно кроме этого не утратить в прочности по отношению к тому металлу либо пластику, что употреблялся ранее. Другими словами его физические особенности должны быть равными либо мало уступать исходному материалу. Тут на помощь инженерам приходят разные конструкции, повышающие жесткость его элементов и кузова, усиления, новые соединения и типы сварки, повышающие жесткость автомобиля.
Во-вторых, исходное сырье должно быть ненамного дороже стандартного материала. Тут уже сложнее. Забрать, к примеру, алюминий, а правильнее его сплавы. Это вправду легкий, твёрдый и по многим параметрам более прогрессивный материал, чем сталь. Плюс ко всему он не так очень сильно опасается коррозии, в отличие от той же стали. НО! Он весьма дорог в производстве. Соответственно цена кузова автомобиля будет выше.
В случае если кузов подорожает, то автопроизводитель будет должен начать экономить на вторых частях автомобиля, дабы его товар остался конкурентоспособным.
Те же самые сложности (но умноженные на три) мы видим и с применением новомодного композитного материала как карбон. Он лишь начал протаривать дорогу в серийном производстве автомашин, но в далеком прошлом и превосходно зарекомендовал себя в автоспорте. Из-за чего так продолжительно им пренебрегали в массовом производстве?
Все упиралось в сложности и дороговизну производства.
Третий пункт вытекает из прошлого. В случае если кузовные элементы будут стоить дороже, при ДТП алюминиевые запчасти кроме этого влетят в копеечку обладателю автомобиля, что кроме этого скажется на спросе на таковой автомобиль. Для чего обывателю переплачивать за эксплуатацию, в случае если возможно забрать менее навороченный, но несложный и недорогой в эксплуатации автомобиль?
И наконец, производство таких машин потребует более сложных и дорогих разработок. Сами осознаёте, что платить в конечном итоге за все улучшения будут потребители.
Кроме того сталь прошла продолжительный путь улучшений и модификаций. Инженеры создали бессчётные сорта высокопрочной стали. Подробности из высокопрочной и ультрапрочной весят меньше чем те же подробности, созданные из простого металла, но наряду с этим они прочнее и легче переносят нагрузки.
По данной причине, при изначальной более большой стоимости за единицу веса, современная сталь с прогрессивной разработкой производства не выйдет за бюджет производства.
Результат: такие материалы как алюминий, магний и углеродное волокно предлагают большую экономию веса по сравнению со сталью, но они через чур дороги чтобы обширно употребляться в простых транспортных средствах.
Инженеры GM при производстве кузовов новых машин объединили разные типы сталей для обеспечения безопасности при проектировании конструкции кузова. Значит, в случае если сталь стала прочнее, автомобиль будет «бетонным»? Далеко не факт. Вы, возможно, ни раз подмечали, что при аварии современные автомобили мнутся как будто бы они сделаны из фольги.
Это не брак, так задумано производителем. Подобным образом срабатывают территории деформации, поглощая энергию удара и уберегая пассажиров от важных травм. В таких территориях не употребляется высокопрочная сталь.
Ее удел создавать силовой каркас около салона автомобиля.
Поведение современного автомбиля в аварии проверяется не в масштабных краш-тестах, а на персональных компьютерах. Десятки миллионов вычислительных часов потребовались для разработки математической модели Cadillac CT6, а также на персональных компьютерах рассчитывались прочностные и весовые характеристики. Программным методом подбирались материалы, каковые должны употребляться в кузове, просчитывалась и испытывалась конструкция кузова.
На выходе инженеры взяли конечный продукт, что при настоящих краш-тестах повел себя совершенно верно кроме этого как это было вычислено в виртуальной модели.
В CT6 употреблялись все виды трюков для понижения веса при сохранении структурной жесткости. Эта модель GM в этом замысле вправду показательна. Лишь представьте, что современный пластик (мы на данный момент говорим не о углеродном волокне) возможно таким же прочным как сталь, основное для него создать нужную структуру. Дженерал моторс создал ее.
Это новая сотовая структура.
GM создало совсем новую архитектуру известную как «Omega Platform». Она оказалась твёрдой за счет комбинации легковесных современных технологий и материалов литья. При жажде вы имеете возможность детальнее ознакомиться с ней в отечественной статье:
Характеристики: Cadillac CT6, его его будущее и секреты
Увлекательное и весьма необыкновенное ответ для серийно выпускающегося седана.
Экономия веса не упирается лишь в кузовную базу автомобили. Процесс поиска откуда бы возможно еще «отщипнуть» грамм происходит в масштабе всей конструкции. Из граммов складываются килограммы.
45 сэкономленных килограмм сэкономят от 1 до 2% топлива. В текущей модели Camaro если сравнивать с прошлой генерации было сэкономлено 181 кг, пользу для кошелька и экологии вычисляйте сами.
Иначе, клиенты желают функционала, и производители машин должны попытаться сбалансировать вес таких элементов как громадные экраны информационно-развлекательных совокупностей либо дополнительных подушек безопасности.
Другие применяемые материалы и технологии смогут уменьшить количество подробностей, нужных, к примеру, для облицовки внутренней панель багажника. У GM они сделаны из магния при помощи технологического процесса, именуемого формирование выдуванием. Магний нагревают до 450 градусов по шкале Цельсия, что доводит его до консистенции жевательной резинки и после этого его нагнетают под давлением в пресс-форму.
Так сложные подробности смогут быть изготовлены в цельном виде, вместо того, дабы скреплять их из нескольких компонентов штампованной стали.
Из-за чего Volvo уверен в том, что у нее окажется сделать собственные машины к 2020 году, самыми надёжными в мире?
Кроме этого, GM взяло на вооружение способ точечной сварки в серийном производстве, разрешающий соединять разнородные металлы, например, алюминий со сталью. Он разрешает избавиться от заклёпок, что придает конструкции громадную прочность и снова же, снижает вес.
К сожалению не все технологии возможно применить в машиностроении в маленький срок. К примеру, углеродные колесные диски GM все еще имеют определенные неприятности с внешним видом и производством, а легкая цельная композитная панель дна кузова, которая возможно имела возможность бы заменить 16 штампованных металлических подробностей до сих пор имеет кое-какие точки напряжения, каковые сводят все разработки на нет. Однако в батарейном отсеке Шевроле Spark была применена как раз такая разработка и сейчас к ней нет никаких нареканий.
Уменьшение массы есть непростой задачей, подводят итоги эксперты GM. Несложно сделать легкий автомобиль, но не так его твёрдым. В нем должны употребляться структурные материалы, а это дорого.
В нем обязан употребляться верный материал в нужном месте и использует его нужно с умом.